High Efficiency Ovens
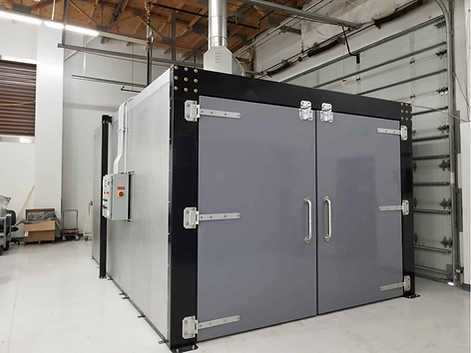



Here are some key features of our high efficiency ovens that will keep you 100% satisfied for the long duration of your operation. The efficiency of our burner, gas train components, flame safety, and airflow design will ensure operating cost savings and the best possible heat processing accuracy available, therefore ensuring that you have the best possible result.
​Air Flow:
-
Our duct design provides a side and up airflow design (see Fig. 1-1)
-
Our air supply duct is located on both sides of the oven and run the entire length
-
Our air return duct is located on the ceiling of the oven and run the entire length of the oven
-
Both return and supply duct have numerous adjustable louvers to ensure even air flow and temperature uniformity throughout the entire oven (see Fig. 1-2)
-
With the correct amount of air changes and adjustments to the louvers, you therefore will obtain maximum temperature uniformity throughout the oven
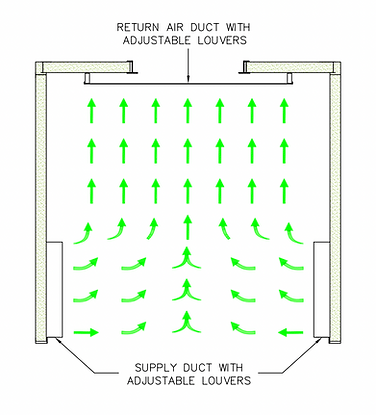
Fig. 1-1

Fig. 1-2
Burner & Burner Box:
-
We use the Maxon Ovenpak series, the Cadillac of all burners — their reputation exceeds their name
-
Forced air burner with a 3/4 HP motor
-
40:1 turndown ratio which gives you more capabilities for temperature uniformity
-
Runs on low gas pressure
-
The Burner Box is built, designed, and engineered to be very durable to withstand the stress of high and low temperatures, but yet lightweight to minimize the stress on the supports
-
Siemens gas train and flame safety system provided
-
We provide a metal filter for the inlet air into the burner box and an adjustable door for ease of air balancing (see Fig. 2-1)

Gas Train:
-
Designed and engineered for minimum pressure drop and maximum flow to the burner
-
Meets NFPA 86 and can be configured to meet IRI standards
-
All high end Siemens, blocking valves, actuators, Proof Of Closure, and modulating motor
-
The Siemens modulating motor accepts numerous types of inputs (e.g. 4…20mA, volts, etc.)
-
Switches, single or double potentiometers are available for position feedback
-
It’s designed for demanding applications with great accuracy and small hysteresis
-
Degree of protection: IP54 or IP65
-
-
Honeywell ignition transformer
-
Burner and gas train factory assembled and pre-wired with wire labels for ease of field installations (Fig. 3-1)
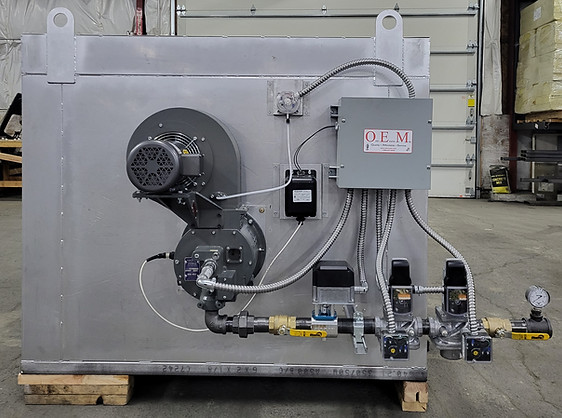
Fig. 3-1
Flame Safety:
-
LCD display on the front door of the UL control panel is the communication interface to the flame safety (See Fig. 4-1 and Fig 4-2)
-
Gas proving system to meet IRI standards
-
Different levels of login to the flame safety to ensure settings are secure and not tampered with
-
User level – minimal changes can be done
-
Technician level – access to features mainly required for maintenance and start up
-
Engineering level – access to all parameters of the flame safety unit
-


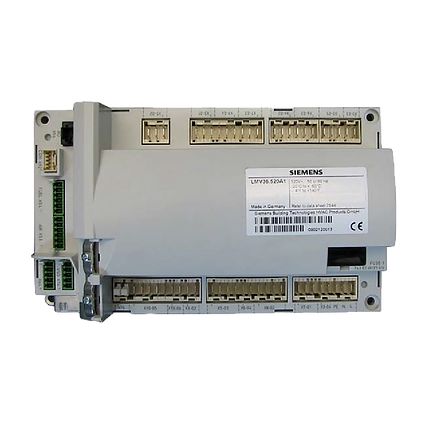
Fig 4-2
The LMV3 is a microprocessor-based system with matching system components for control of the forced draft burners with medium to high capacity.
​
The following system components are integrated in the LMV3 Basic Unit:
-
Burner control with gas valve proving system
-
Electronic air/fuel ratio control with a maximum of 2 actuators
-
Control frequency converter air fan
-
Modbus interface

Example: Modulating gas burner
The system components display and operating unit — actuators are connected directly to the LMV3 basic unit. All Safety digital inputs and outputs of the system are monitored by contact feedback network (CFN).